Lorsque les conditions menant à la combustion deviennent suffisamment chaudes – température de l’air d’admission, température de la surface de la chambre de combustion, temps requis pour la combustion, taux de compression, etc. – la combustion peut ne plus consommer en douceur la charge d’air comprimé de la bougie d’allumage jusqu’au cylindre mur. Au lieu de cela, vers la toute fin de la combustion, alors que la charge fraîche sur les bords de la chambre atteint une température critique, de minuscules volumes peuvent s’enflammer automatiquement. C’est la détonation, également connue sous le nom de cliquetis.
Notez que le cliquetis n’est pas une pré-inflammation, qui est une combustion qui commence avant l’étincelle d’allumage, déclenchée par la présence de quelque chose de chaud dans la chambre – une électrode de bougie surchauffée ou un dépôt de carbone incandescent. Le cliquetis ne se produit que vers la toute fin d’une progression autrement normale de la flamme de la bougie d’allumage à la paroi du cylindre. C’est pourquoi celui-ci endommage les bords extérieurs du piston, tandis que le pré-allumage perce généralement un trou à travers le centre de la tête du piston.
Ces derniers poches de mélanges dans la chambre de combustion, chauffés à une température critique, ont été modifiés chimiquement de manière à transformer le mélange en un explosif sensible. S’il s’enflamme automatiquement, il brûle à la vitesse locale du son (1500m/s ou plus), formant ainsi une onde de choc violente qui peut projeter de l’aluminium sur le piston, et qui frappe les surfaces métalliques avec un impact audible, d’où le terme « cliqueter », parcourant la protection thermique normale d’une couche limite de gaz stagnant et accéléreant la transmission de la chaleur de combustion dans ces surfaces métalliques.
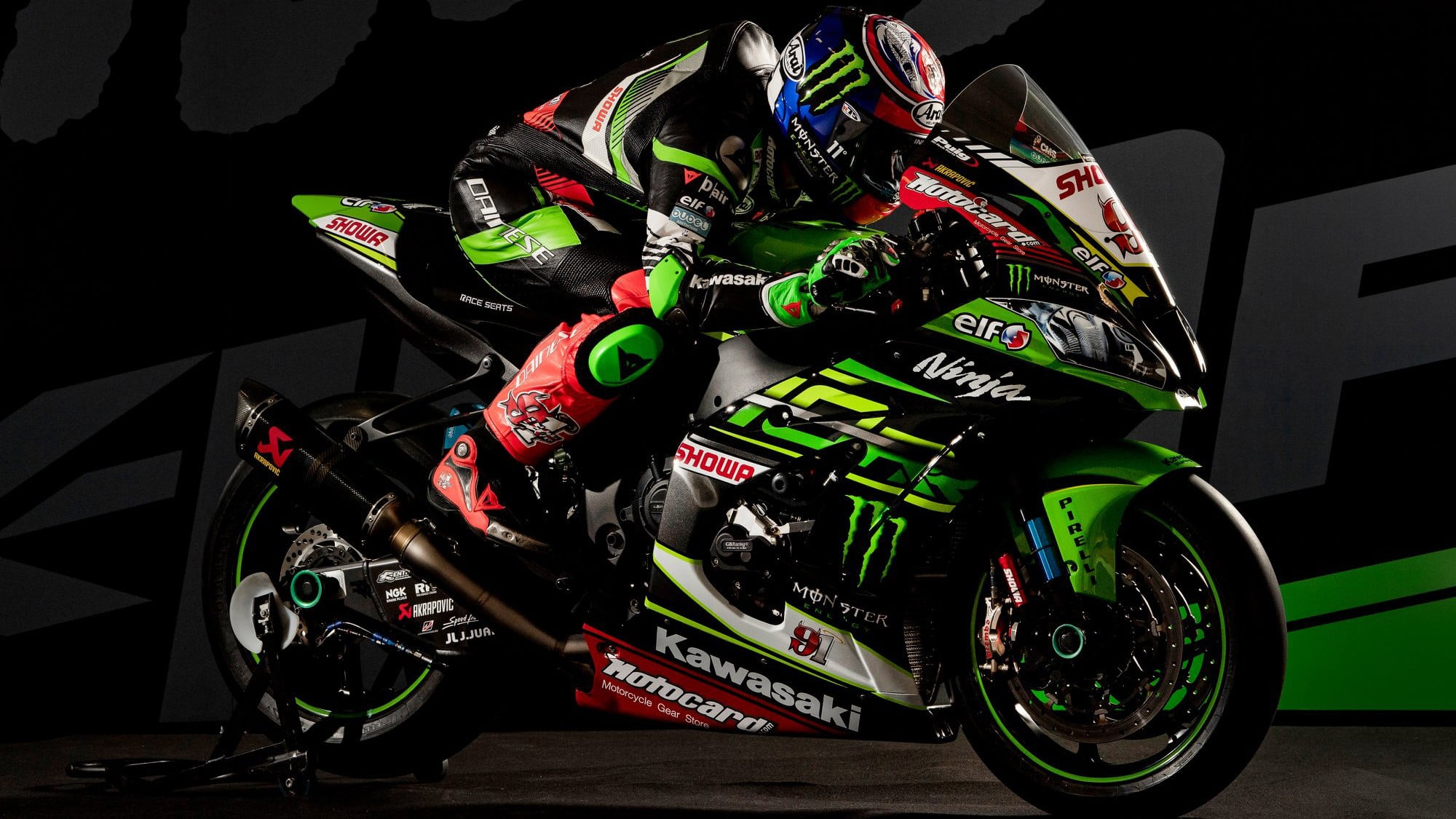
Le ZX-10RR de Kawasaki, vainqueur du championnat WSBK, trouve ses racines dans le Z1 à quatre cylindres des années 1970.
Les pilotes des Yamaha TZ250/350 des années 1970, remarquant une augmentation soudaine et inexpliquée de 5°C de la température du liquide de refroidissement, savaient que leurs moteurs avaient probablement commencé à cliqueter. Si ces motos avaient été équipées de thermocouples pour mesurer les températures des gaz d’échappement, ils auraient en même temps vu une baisse de celle-ci. Pourquoi ? Avec plus d’énergie de combustion pénétrant dans les surfaces chaudes du piston et de la chambre, cela abaisse la température de gaz d’échappement.
Pour de meilleures informations sur le fonctionnement du moteur, les pilotes ou les metteurs au point démontaient le piston après chaque entraînement, et certains démontaient le cylindre également, permettant un examen minutieux de haut en bas des pistons pour prévenir tout signe possible de détonation ou de température de fonctionnement anormale.
Lorsque l’additif antidétonant à base de plomb, le plomb tétraéthyle (TEL) a été interdit dans l’essence de compétition à la fin des années 1990, Yamaha a réagi en fabriquant ses propres culasses en cuivre, qui conduisent la chaleur nettement mieux que l’aluminium. Les ingénieurs ont également doublé l’épaisseur des têtes de piston, abaissant la résistance au flux de chaleur du centre de la tête chaude vers la paroi du cylindre beaucoup plus froide. Ces mesures, en réduisant la température du métal en contact avec la charge fraîche, ont réduit la quantité dont le taux de compression a dû être réduit pour faire face au carburant sans plomb obligatoire moins résistant aux chocs. Le plomb tétraéthyle a agi comme un catalyseur à taux négatif, ralentissant la transformation chimique entraînée par la chaleur de ces derniers morceaux de charge fraîche en un explosif sensible.
En 1944, alors que les bombardiers américains B-29 entraient en action dans le Pacifique, les incendies de moteurs au décollage ont été un grave problème. Dans le but de permettre les décollages de ces avions à trois moteurs, des compresseurs plus performants ont été testées. Mais c’était peine perdue : le refroidissement à air marginal de ces moteurs Wright R-3350 les faisait exploser à une pression d’admission de 3.5 bars. L’équipe de développement voulait donner aux équipages 2.600 ou même 2.800 chevaux pour permettre de décoller en urgence dans des conditions de guerre, mais même avec un enrichissement en carburant de 20% pour refroidir par évaporation la charge entrante et avec quasiment 2 grammes d’additif plombé antidétonant par litre de carburant, la limite du cliquetis était déjà atteinte.
Mais alors comment les athlètes arrivent ils à dépasser leurs limites, mais pas les moteurs ? Il n’y a pas moyen de dépasser le martèlement destructeur du cliquetis et la perte constante de matière des pistons, ce qui peut laisser les segments de piston s’avancer dans un espace vide qui était quelques minutes auparavant en aluminium solide.
Si l’on compare les moteurs des Kawasaki Z1 de 1982 (1000cc, préparée pour le Superbike) et celui de l’actuelle ZX-10RR de Superbike, avec sa puissance estimée à 230ch, on note que dans ces deux moteurs, la BMEP (Brake Mean Effective Pressure – pression moyenne appliquée uniformément sur les pistons de haut en bas de chaque course motrice, produisant la puissance réelle du moteur), est très similaire : 14,61 et 14,13 bars.
Mais à l’époque des Z1, le régime maximal était fortement limité. Ces moteurs étaient équipés de bielles dont les roulements à rouleaux et à billes étaient pressés, et étaient fiables à 10250 trs/min, mais qui dont leur ajustement se désolidarisait à seulement 750 tours plus élevés. Pourtant, ces ajustements à la presse étaient soudés.
La vie n’est pas automatiquement parfaite simplement parce que le moteur ZX-10RR actuel a une bielle en acier forgé d’une seule pièce fonctionnant dans des paliers lisses super rigides. Pour faire fonctionner ces bielles à 15.000 trs/min, le système de graissage doit garantir qu’aucun air n’est pompé avec l’huile et cela a nécessité une ingénierie intensive.
La bielle d’origine peut-elle gérer l’augmentation de près de 60% du niveau de stress résultant de l’augmentation de la zone rouge de 12.000 à 15.000 trs/min? Ou des fissures apparaitront elles dangereusement ? Chaque partie d’un moteur de course doit avoir une durée de vie connue et garantie en heures, surtout maintenant que les règlements exigent que les moteurs durent plus d’un week-end de course. Il est peut-être temps de penser à utiliser des matériaux plus résistants pour la bielle, qui seront logiquement plus chers.
On peut également accorder une attention minutieuse à la finition de la surface de chaque partie arrondie qui relie un tourillon de vilebrequin à la partie de vilebrequin adjacente. Il est nécessaire que ces filets soient laminés et nitrurés, ce qui les met en compression locale qui les protège des contraintes de traction/étirement propagées par les fissures.
Lorsque vous corrigez un problème qui limite le chemin vers une puissance et une fiabilité accrues, un autre problème apparait. Lorsque le temps est compté mais pas l’argent, toutes les solutions possibles doivent être abordées simultanément, pas l’une après l’autre. C’est vraiment très cher, mais c’est aussi comme cela que les moteurs de fusées F-1 sur Saturne V ont été réalisés à temps pour accomplir cette mission historique de 1969 sur la lune.